After decades of glass thickness reduction and transparency in glazed façades, a whirl of glass translucency and weight is taking the architectural scene. You may have found it already in small places: building entrances, sculptures and the like. But the quest for thick, icy blocks of glass stacked in façades is here to stay, or at least that's my impression.
This post will discuss origins and directions of the 'thick glass' trend.
 |
GE Building glazed entrance detail, seen from inside. Designed by Lee Lowry, 1933-34 |
Inspiration for this story came by chance during a visit to New York City some months ago. The main building at
Rockefeller Center - RCA tower, now called GE Building - has a decorated main entrance finished in 1934 that called my attention. The top part of the entrance shows three stone low-relief panels conmemorating the spirit of the radio, named "Wisdom, Sound and Light" (see image below).
Sculpted by
Lee Lawrie, the imposing central panel showing a bearded Wisdom figure, today an art deco icon, can be clearly seen from Fifth Avenue. But the top limestone pieces are only part of the story.
 |
GE Building entrance at the Rockefeller Center - stone and glass low-relief by Lee Lawrie, 1933-34. You can identify Wisdom at the top centre, Sound at the left and Light at the right hand. |
With golden rays crowning his head, Wisdom's right hand clutches a golden compass that measures the cosmic forces swirling in the 15 x 55 feet glass blocks screen below. Here comes the magic. Made of 240 glass blocks carved in cast Pyrex, the screen is a technical and artistic masterpiece.
 |
Piccirilli's "Youth leadind Industry" at 636 5th Ave |
The glazed bas-relief is a translucent wall of rectangular glass pieces (around 700 x 450 mm each), tied at their back to vertical bronce stripes, with a delicate front texture: calmed at the edges of the screen, agitated in the central axis below the moving compass. The attached images (see below) provide a pale impression of its contrasts: thick but slender, translucent from inside but almost opaque from outside, half part of a door and half part of a sculpture.
Lee Lawrie was not the only artist using cast glass at the Rockefeller Center in the thirties. If you compare Lawrie's magnificent glazed entrance with Attilio Piccirilli's "Youth leading Industry" (see at left, finished in 1936) the contrast is clear. Piccirilli's glass low relief adorns the entrance of the International Building at 636 Fifth Avenue. Lit from behind but opaque if seen from the inside hall, it remains an evening spectacle on Fifth Ave. Piccirilli's bas-relief was cast in 45 Pyrex glass blocks, each hand-cast and different.
Good enough, but we will probably agree that Piccirilli's screen is merely decoration, not architecture. Glass here could have been marble and it would remain rather similar. That is not the case with Lawrie's screen, where glass and transparency go hand in hand as the following images taken from inside testify.
 |
Top to bottom: details of the glazed wall at the Rockefeller GE Building entrance. All taken from inside except the bottom right one. |
Seen from today Lawrie's glazed entrance is strikingly modern. In fact, a number of translucent massive facades could be linked to the images above. One of them, of course, is Rafael Moneo's
Kursaal Auditorium in San Sebastian.
The Kursaal Auditorium is the combination of two translucent, twisted and slightly angled glass cubes located by the seaside - two 'stranded rocks which perpetuate the geography and underline the harmony between the natural and the artificial'. The cubes have curved laminated glass walls which protect them from salt-laden sea winds. The outer skin, a laminated 19 mm extra-clear, sandblasted glass with an external 5 mm fluted printed glass, transmits light to the interior by day; at night the exterior is transformed into a mysterious light source.
 |
Kursaal San Sebastian (Rafael Moneo, 1990-1999). Main Auditorium building looking outside through one of the big windows. |
I like the view from inside the cubes (see above) because it explains the building concept better than the typical daylight external images. Of course there are differences with the GE building entrance. First in scale, then in layers: the Kursaal façade is a double skin wrapping the steel structure of the buildings. The outer skin is curved and fluted, the inner skin is flat. Both are slightly translucent to avoid direct vision of the encased steel structure.
 |
Kursaal San Sebastian. The curved glass facade. |
But there are a number of surprising similarities too. In both cases the glass grid is rectangular and horizontal, with continuous vertical joints - a stacked bond. The intention is not to read the facade as heavy masonry but as a light screen. Then the curvature: concave at the outside, flat at the inside. And finally the fixing system: a slender line of mullions from behind in both cases. Even the yellow light coming in is strikingly similar!
The images of the Kursaal facade during construction (see below) are as always very instructive. Isn't this Lawrie at a gigantic scale?
While I was working for Cupples - around 1992-93 - we visited Rafael Moneo at his studio in Madrid for this project. He was rightly obsessed with the quality of fluted glass he was looking after, and with the availability of suppliers for such a combination of fluting, lamination, extra-clarity, translucency and bending in glass. Cupples presented Moneo several glass samples and we prepared some façade details. The story moved on and finally Cricursa supplied the glass. The façade contractor was the Basque group Umaran, like Cupples a great but extinct dynosaur from the 20th century.
 |
Kursaal San Sebastian. Images of the double skin façade during construction. |
But Moneo's Kursaal use of glass is also an example of relative failure in translucency. Depending on the time of day and the sun position the structure behind the outer glass may become too obvious. In these occasions the visual impression is not of an ice block but of a thin veil: the game of scale is lost and the building fabric becomes too evident. The image below is one of those cases.
Thick glass can be more subtle and difficult to control that sheer transparency... but then, when is glass really transparent?
 |
Kursaal San Sebastian. Aluminium mullions and main structure appear behind translucent glass as seen from outside. |
Let's go back to New York in our quest for iced glass blocks. 11 Times Square is a new office tower (opened in 2011) located right beside Renzo Piano's New York Times building. Waiting for the green light at 8th Ave with 41st Street I was surprised by the contrast between a tall, thin, mullion glass-supported transparent wall and a back-lit stacked glass wall beside. Both are part of the main lobby of this tower.
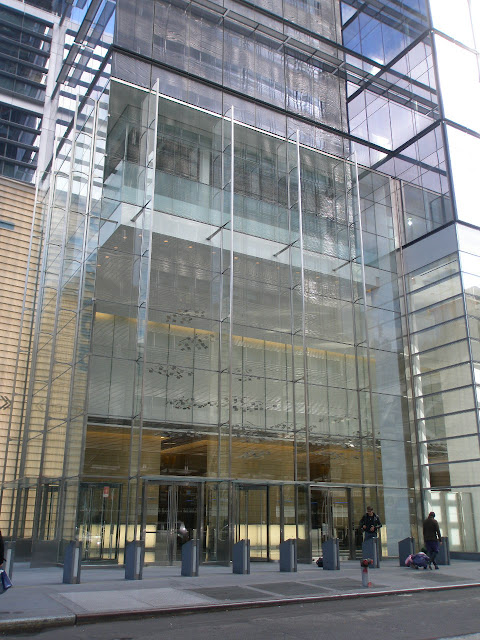 |
11 Times Square lobby seen from 41st Street, NYC. FXFowle Architects LLP. |
If you came from a time travel - right from the seventies for instance - you would be surprised by the height of this transparent glass wall, standing still without any apparent aluminium or steel support. And it's really impressive, even today! But after the last two decades of structural glass walls we are used to see large glazed walls supported by glass fins with bolted stainless steel spiders as the only connecting points.
What called my attention in this case was the yellow glass wall to the left of the lobby: a back-lit translucent wall made with flat, vertically fluted glass blocks, stacked to provide a screen to support the building name and its tenants. It reminds us the facade of the Kursaal or Lawrie's cast glass, except that this one is opaque and flat. A detailed view can give us more clues. The whole glass lobby was commisioned to Gartner Steel and Glass, part of Permasteelisa Group, and completed in 2010.
The transparent part has a surface of 1,040 m2. The glass fins project out of the glass plan into the walkway and are 16.4 m in height, helped by an intermediate connection at a back slab located at 2/3 of their total height. The special stacked glass wall - this is all I found at Gartner's webpage - is 120 m2.
 |
11 Times Square stacked glass wall at the lobby. Images from outside (left) and inside (right). |
A detailed view will give us more information about our next icy translucent wall. It must be a laminated glass with the outer lite cast in vertical stripes. The thickness of the stripes is wider than the one at the Kursaal, but its flatness provides an impression of subtle weaving. As in San Sebastian the glass is retained by a grill of parallel, horizontal profiles: here they are in stainless steel, those at the Kursaal are made in cast aluminium. What a decision of a master builder: cast aluminium supporting cast glass!
The stacked glass wall makes itself apparent in the evenings, when crowds rushing to attend Broadway plays mix with those running home from work. At this time the 'eleven' mark behind the glass becomes obvious and the tenants' names shine in darkness against the back-lit wall. Sadly, this is a sign of our times: gone are Wisdom and his colleagues; what matters now is company brand image...
 |
11 Times Square tower. General image (left) and lobby from inside (right). The stacked glass is a screen supporting tenants' logos. |
The list of recent 'thick glass' walls is endless and this post cannot be that long. From the examples above we have got a fair view of stacked, heavy laminated glass, but this is only one technique in many.
Let me list other techniques that are being used to obtain the impression - or the literality - of thick glass (some of the buildings listed here are shown right below):
- Fused glass. A supplier of this technology is Fusion Glass Designs, a brand of the British company Chelsea Artisans. One of their recent jobs is the Louis Vuitton shop in Singapore, with kiln formed, curved and laminated glass. You can also look at this webpage for more info.
- Molten cast glass. This is the way U-glass (or channel glass) panels are made. The European main name in this technique is the German firm Lamberts, with the brand name Linit, while its US counterpart (and business partner) is Bendheim Wall Systems. The exemplary building with a U-glass cast facade is of course the Bloch Building at the Nelson-Atkins Museum of Art in Kansas City, a project of Steven Hall Architects finished in 2007.
- Slumped cast glass. Also called warm glass or kiln forming, a supplier of this technology is the British firm Warm Glass.
- Cast glass. The general term; many of the examples here are somehow made of glass cast in a mould. A well-known supplier is Castglass and one of their recent jobs, the Diesel store in NYC, with cast glass molding in LED lighting. Another façade to visit is their Glassworks Hot Shop in Louisville Kentucky.
- Pattern glass. A general expression for laminated or printed glass where an intermediate layer or screen is added, creating the impression of pattern and providing translucency. A high-quality European supplier of this kind of glass is GlasMarte from Austria. They are the glass suppliers and façade contractors for Peter Zumthor's acclaimed translucent façade of the Kunsthaus in Bregenz. They also have an interesting glass point ceiling fitting system, named GM Kub. Worth having a look...
- Recycled glass. A new technique. When glass pieces coming from recycling are fused the result is a greenish, opaque panel with a promising application to façades. For most cases a 20mm thickness provides the required strength. See more at the British supplier The Greenhouse Effect.
- Other techniques, worth exploring if you are interested: glass billet, heavy laminated glass (the buildings presented above), carved glass, extruded rolled glass, textured glass...
 |
The Louis Vuitton facade in Singapore. Kiln-formed, laminated and curved 8+8mm glass. |
 |
Nelson Atkins Museum of Art, Kansas. Steven Hall architects. U-glass facade from Lamberts - Bendheim. |
 |
Nelson Atkins Museum of Art; Steven Hall architects. Detail of the double skin facade with U-glass at the outer side. |
 |
Kunsthaus Bregenz, Peter Zumthor. Austria 1997. Etched translucent glass. |
 |
The Kunsthaus at dawn with back-lighting. |
We are entering a different ground here, that of glass as an artistic expression. But don't be afraid. If 'thick glass' in its many forms shall remain a trend for contemporary façades, there must be artists out there, chaps comparable to Lee Lawrie, from whose work we could get inspiration. You can find many names in this useful
link provided by Lamberts. But if you wanted to meet only one name that must be Danny Lane, the best one to finish this post, an invitation to the artistic glass world.
 |
Danny Lane posing at his studio in London. |
Danny Lane (born in 1955) is an American glass sculptor living and working in the UK. Lane’s work is monumental as much as physical; his stacked and fractured glass walls are in a transition zone between scupture and architecture. His London studio is equipped to create works of considerable scale, in glass and in steel. Glass furnaces enable Lane to create works of fluidity and brilliant colour as the ones selected below.
Go and visit his webpage for more. Please click the
Process tab: you will learn how these glazed, iced pieces were made.
 |
Danny Lane, detail of stacked glass with a tensile rod. |
 |
Danny Lane, Presence of Seven. Allegheny College Pennsylvania USA (2002) |
 |
Danny Lane, Stairway. Borgholm Castle, Sweden (2005) |
 |
Danny Lane, Split Prism. San Francisco USA (2011) |
 |
Danny Lane, Borealis. General Motors HQ, Detroit USA (2005) |
 |
Danny Lane, Borealis detail. General Motors HQ, Detroit USA (2005) |
 |
Danny Lane, Ice. San Francisco USA (2011) |
Is there materiality in glass? Plenty, as we have seen. Why then should we go only for the thin, transparent, ephemeral glass lites we have been using during the last century? Come on, cross the new frontier and be welcomed to the thick glass world...
65 comments:
Ignacio, thank you for including Bendheim Wall System's Bloch Building designed by Steven Holl in your standout list of projects.
Marc Fink, Bendheim Wall Systems
Common types of glazing that are used in architectural applications include clear and tinted float glass, tempered glass, and laminated glass as well as a variety of coated glasses, all of which can be glazed singly or as double, or even triple, glazing units.
Nice blog here! Also your website loads up fast! What web host are you
using? Can I get your affiliate link to your host? I wish my
site loaded up as fast as yours lol
Look at my website seo ()
Great post. I was checking continuously this blog and I am impressed!
Very helpful information specially the last part :) I care for such
info much. I was looking for this particular info for a long time.
Thank you and best of luck.
my page; photo booth west london
I am actually pleased to read this web site posts which consists
of plenty of useful data, thanks for providing these
information.
My weblog - raspberry trim reviews
The New York Pass is a 'smart card' - like a credit card with a computer chip inside - which allows you completely cash free admission to more then 80 popular New York tourist attractions.
Article is very informative and well written .Thank you for sharing it .We Vtechengineers offer solution on different variety of structural works and acp cladding works in PuneClick here
You are so great in contextualizing the concept! Amazing work indeed. Very inspiring and moving. Thank you for sharing this work of yours. Meanwhile. If you are interested and looking for curtain fabrication services
singapore
you may visit our website. You can also check our available services to offer. Thank you and Godbless!
Reading this piece, i never thought that I can be inspired like this. Amazing! Your works are very credible enough.. Meanwhile. If you are interested and looking for "curtain fabrication services
singapore"Feel free to check and visit our site and look for our affordable items with a very nice quality. Thank you and Godbless!
Amazing piece. There is so many lesson to be learned from this. Thankyou for sharing this kind of work author. Randomly speaking, are you looking for a blinds fabrication Feel free to visit our website. Thank you and God bless!
Thank you for making this astounding article, informative and knowledgeable!! We have so much to learn from this. Anyway, If you are interested and looking for
curtains and fabrication service Singaporeyou may visit our website. You can also check our available services to offer. Thank you and More power!!
Your work is very engaging! Amazing piece and is worth reading and sharing. Hoping for more of this kind of work of yours author. Meanwhile. If you are interested and looking for blinds fabrication services SingaporeFeel free to check and visit our site and look for our affordable items with a very nice quality. Thank you and Godbless!
Good work, Well detailed and explained by the author. Hoping that it will inspire more readers. Thank you for sharing this author. Randomly, blinds fabricator Singapore our company offers service at a very affordable price, feel free to visit our website if you are interested. Thank you and Godbless!
Good work, Well detailed and explained by the author. Hoping that it will inspire more readers. Thank you for sharing this author. Randomly, blinds fabricator service our company offers service at a very affordable price, feel free to visit our website if you are interested. Thank you and Godbless!
Good work, Well detailed and explained by the author. Hoping that it will inspire more readers. Thank you for sharing this author. Randomly, blinds fabrication services Singapore our company offers service at a very affordable price, feel free to visit our website if you are interested. Thank you and Godbless!
Nice article. Highly recommended. The thoughts are clear and well explained. Thankyou for sharing your work, truly worth reading. On the other hand, if you’re interested in , curtains and fabrication service Singapore, feel free to visit our website. Thankyou and Godbless!
Amazing Content, Thanks for sharing.
Structural Analysis in UK
I’m having a fortnight meeting in USA so my stress reliever is reading some blogs, but it’s quite difficult for me to spend or waste my time in simple blogs or non sense writings then somehow I read your works It’s so confusing because I love your enthusiasm on this subject so I comment on to admire your style. It happens that I’m curious about blinds fabricator Singapore, I think you should try to check it out!
You Have Impeccable Manners of writings. When you feel gutted to someone or anything, Just continue your work be proud of yourself, because your an inspiration for me, Thank you for being you. Did you visit blinds fabricator Singapore you should try it!
You Have Impeccable Manners of writings. When you feel gutted to someone or anything, Just continue your work be proud of yourself, because your an inspiration for me, Thank you for being you. Did you visit blinds fabrication services Singapore you should try it!
Thanks for your information; you have such great knowledge on these criteria. It’s really helpful to me. Aluminum Composite Roof Singapore
You have been discovered it then you share it with your readers, I’m grateful because I’m one of your readers, I learn a lot from your posts, hope I will be able to read more. Do you have any idea about blind singapore? I'm really curious about it.
You Have Impeccable Manners of writings. When you feel gutted to someone or anything, Just continue your work be proud of yourself, because your an inspiration for me, Thank you for being you. Did you visit curtain fabrication services Singapore you should try it!
Cotton ware is one of the trusted leading blinds fabricator service company, who can give you a quality and excellent service.
Cotton ware specializes in customizing window treatments for residential and commercial establishments. We fabricate various types of curtains such as day curtains, night curtains, and blackout curtains. We also do all sorts of window blinds fabricator Singaporeand we perform sofa and chair re-upholstery.
Are you tired of finding the shop where they offer a good and quality service? Don't worry cotton ware is here to help you in your blinds fabricator Singapore. Where you observe the excellent and quality service that cotton ware can give it to you.
blinds fabrications services is one of the most famous services that Singaporeans avail but it is very hard to find a company who will give you an excellent service. Don’t worry cotton ware offers a cheap but a very excellent service for your blinds,
Cotton ware is one of the trusted leading company that offers blinds fabricator service, who can give you a quality and excellent service.
Cotton ware is one of the trusted leading company that offers blinds fabricator service, who can give you a quality and excellent service.
Let cotton ware help you in your blinds fabrication problem. Cotton ware offers the cheapest but excellent blinds fabrication services.in Singapore.
A debt of gratitude is in order for giving such helpful data. I am particularly intrigued with your article the End of lease cleaning House | Bond cleaning Western suburbs and I am glad that I am related with your site.thanks! Respects,
You never want to be looking anywhere but local for a roof repair gainesville georgia. I don’t know if they will charge you more, but like you said, they will know the regulations and building codes better. I have never thought about getting a warranty for the roof. I would see if you actually need a warranty because my house for instance is in the desert so we don’t get very violent storms like other places. (edited)
Cotton ware blinds fabricator service singapore is one of the trusted leading laundry company, who can give you a quality and excellent service.
Are you tired of finding shops that can offer good and quality services? Worry no more, cotton ware is here to help you in your blinds fabricator Singapore. Here, you can observe excellent and quality services that cotton ware can give to you.
Kaspersky Help Number UK – Kaspersky antivirus software has a lot of advanced techniques and features associated with the workings of the software. If in case these techniques are troubling you such as if you are not able to install the software or if there is some other issue with the workings of the software then in that case it is advisable that you get connected with the team of experts.
Kaspersky Support Number UK
Kaspersky Help Number UK
Kaspersky Customer Service UK
Kaspersky Contact Number UK
If Bullguard is to be installed on an additional device then, in that case, log in your Bullguard account on the device on which Bullguard antivirus is to be installed. If you still need more information regarding the installation procedure then, in that case, it is advisable that the user gets connected with the team of trained and certified Bullguard experts.
Bullguard Support Number UK
Bullguard Help Number UK
Bullguard Contact Number UK
Bullguard Phone Number UK
Bullguard Tool Free Number UK
Bullguard Chat Support Number UK
Bullguard Customer service Number UK
Bullguard Helpline Number UK
Choosing things that you want to wash is one of the best tips for laundry firms.
dry cleaning services
Is your blackout curtains singapore are shabby and old? Don’t worry cotton care offers a curtain cleaning service where you will see the excellent quality result.
rug cleaning
This blogs about the best online reputation management is quite interesting, I think I should take time to read more of your works maybe I can find more interesting blogs! Thank you for writing a unique blogs!
What a fabulous writings! I think I should consider this as a reference for my research about reputation management services because nowadays lots of companies are curious on how they manage their reputation especially when it comes to technological changes.
In managing your online reputation, you need to build your website and your connection to your audiences and I think this writing of you author made my day! This is very nice and full of learning!
You really got a fantastic ideas about social media reputation management! And it is really helpful because nowadays it’s hard to maintain your reputation, especially in social media.
Were you tired of finding shops where good high professional products could be offered? Don't be afraid, cotton ware is here to help you out in blinds fabricator service singapore. You can see here the excellent and high-quality services that cotton ware can offer you.
curtains and fabrication service Singapore are form of window treatment and it completes the overall appearance of the house.
seo services that target different searches such as image searches, video searches, educational searches, news searches and vertical search engines unique to the industry.
A web developer must know the knowledge that you shared to us, they must see your work because they can learn from it. I suggest that you should visit also azaza website because it also has a more relevant information that can help you.
Since social media marketing is now one of the most trending topics all over the nations, it is really helpful for every individual to have some time reading trending blogs and keep themselves updated for the changes happening in every part of the country every year.
This is a very interesting topic about administrative support services, many companies would not able recognized the good thing in having this in their consideration for their growth especially in sales.
This blogs is really favorable to me, because I’m searching for some insights about virtual assistant company that might be use as reference in the future. Thanks a lot author!
This is ridiculously awesome! I don’t have any ideas about online reputation management but it looks like to me based on your blogs, that you are clearly an expert on this topic! And it was an advantage for me to read your work! I will keep this!
Cotton ware is a shop which offers good laundry services that classifies the items they serve to ensure that each item is properly laundered. Cotton ware helps you to produce the excellent curtain fabrication, a type of window treatment that completes the overall look of the building….
curtains and fabrication service Singapore are form of window treatment and it completes the overall appearance of the house.
Interesting Article. Hoping that you will continue posting an article having a useful information. property inspections sydney
Really it is nice and informative and helpful blog for more relevant information. This is just the kind of information that I had been looking for. Thanks for sharing informative Blog. If you want to HP wireless printer setup support, this blog is a must read. We are a team of HP professionals who assist HP users 24/7 in handling a variety of issues.
This is very informative post, good work, i like this blog and wish to read more from you. thanks for such a informative post. i also like to share some useful links! It’s not a tough task to activate Roku. Understand the Roku activation steps. Connect the necessary hardware. It's the power and HDMI, USB cable that is required. Sign in to Roku account and move to the page Roku tv link code.
glass façade - Welcome to Sunnyquick, We are a specialist manufacturer of glass curtain wall, aluminium windows and aluminium doors. We provide the best glass facade, aluminium facade, aluminium windows and aluminium doors. Contact us now - 0086 134 3025 9282
Thanks for sharing your experience with us. I am also looking for building glass repair service for my office building.
I love how you've incorporated the information on facade into the design of this glass. It's a great way to highlight the building's unique architecture and make it more memorable. infinity is a great choice for any building that needs to be seen from the outside.
The trend of thick glass is inspired by Rockefeller Center's main entrance. The entrance has been covered with a huge piece of glass that was used to protect the building from the harsh New York weather.
The "thick glass" trend is a new type of interior design that is becoming popular in the United States and China. It is characterized by a large amount of windows, which can be seen everywhere in homes, offices, and hotels.
The trend has been inspired by the Rockefeller Center's main entrance. The entrance has been covered with a huge piece of glass that was used to protect the building from the harsh New York weather.
Best high quality glass suppliers in Palakkad, Kerala
Fluted glass is such a fascinating design choice! It not only brings a vintage charm but also adds a contemporary twist to decor. I recently explored some beautiful fluted glass items on Quartier Studio, and I was impressed by how they can transform a simple space into something truly special. The play of light and shadow through the grooves creates a warm ambiance that’s hard to resist. Has anyone else experimented with fluted glass in their interiors? I'd love to hear about your experiences.
I love the podcasts available on this site.
Visit for - Architectural Glazing
Post a Comment